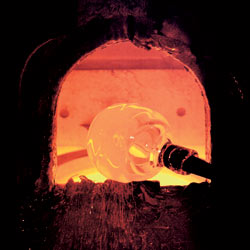
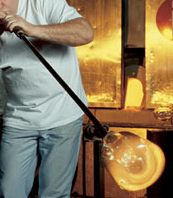
Our Studio
The glass is purchased, primarily in sheets, and hand selected for compatibility. Each design idea is drawn and tested by fusing structural and color samples. Kiln shelves and mold must be prepared for those styles requiring shaping (such as bowls). Molds may be stainless steel, but more often are hand-formed out of clay or refractory materials. They must dry for 3-5 days, be sanded for a smooth finish, be bisqued in the kiln, and specially coated so the glass does not adhere.
Most pieces require several separate kiln-firings, with some limited edition work requiring up to six separate firings. Each color, style and texture of glass requires different heat levels and different soak periods. Each stage of the firing process is critical to the outcome.
The first stage, after the design has been cut out of glass, is taken up to 1525 degrees. It takes from 6 to 15 hours to reach the desired temperature, and another 12 to 20 hours to cool, dependent on a number of factors.
How quickly, or slowly the temperature must be taken up or down is determined by the thickness of the glass, how many firings it will endure, and for what function it will serve. For greater durability, the glass must be properly annealed for re-stabilization of the transforming molecules. This can be a slow process. The operation of the kiln is itself an art form. Twenty second too long at temperature will ruin pieces like the Tiered Menorah (MTL). The amount and length of heat influences the color, the finish and the texture. The understanding of the relationship between glass and heat; movement, shrinkage and expansion, is a skill developed only through time and experience, and greatly effects the finished product. The desired outcome dictates the precise technique employed.
The next stage may involve adding additional design elements, some using lampworking techniques and some using blown glass techniques, where the glass is melted at temperatures up to 2400 degrees. Another stage may involve cutting the fired piece into the desired shape, and then firing it again to attain polished edges. Some pieces may be sandblasted and then re-fired, and some pieces will require re-fusing at a different temperature to attain a different effect.
Any lettering on the pieces are CUT OUT OF GLASS, making our work non toxic and food-safe. They will never tarnish or fade. Some pieces are manipulated when they reach full temperature. This is accomplished with the aid of full arm, high temperature gloves and sometimes steel rods. The slumping, gaining its shape, is next. A lesser heat is required to form the shape, usually around 1225-1275 degrees.
This description has been oversimplified. Even choosing the glass for compatibility is of utmost importance. If incompatible glasses are fused, they could break, crack or shatter. And sometimes this will happen only months down the road, which can even be dangerous. Or perhaps a small foreign particle or drop of moisture ends up between two layers of glass and causes a huge bubble to destroy the creation. Once the piece has cooled from its last firing, there is still finish work which varies from piece to piece.
Working with glass is like doing a dance, very structured, yet free-form... The beauty, richness and luminescence of the glass are all-inspiring. The most exciting part of this creative process is, after all the firings, opening the kiln: all the waiting, the final cooling, and at last, viewing the final product.
© 2009 Zohar Glass all right reserved. Design by Central Point Solutions.